How to Measure the Strength of Hardware Nuts
Hardware nuts, the unsung heroes of construction, play a pivotal role in fastening two or more components together. They provide invaluable strength and stability, ensuring that our structures remain securely in place. However, not all nuts are created equal.
Various factors determine the strength and quality of these essential fasteners. In this post, we will delve into the crucial topic of measuring the strength of hardware nuts, a subject that is of utmost importance to engineers and construction professionals.
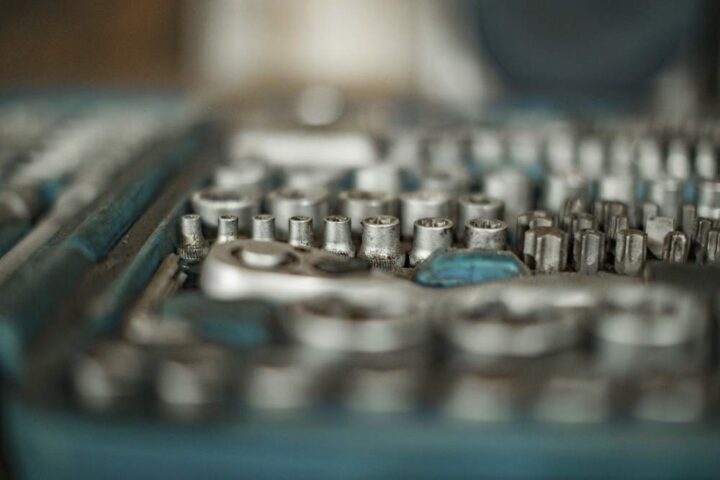
Tensile Strength
One of the most critical factors in determining the strength of hardware nuts is their tensile strength. This measurement indicates the maximum pulling force a nut can withstand without breaking or deforming permanently.
The higher the tensile strength value, the stronger the nut. To measure tensile strength accurately, specialized testing equipment applies an axial pull to the nut until it reaches its breaking point. The force required to break the nut determines its tensile strength rating.
Yield Strength
While tensile strength helps understand when a nut fails under tension, yield strength measures how much stress a nut can endure without permanent deformation or elongation. It represents the maximum force a nut can handle before transitioning into plasticity.
Yield strength testing involves applying pressure to a nut while monitoring changes in shape and size; it stops just before permanent deformation occurs. The recorded force during this test determines yield strength.
Hardness
The hardness of a nut measures its resistance to indentation or scratches caused by external forces. A harder nut tends to be more durable and resistant to wear over time.
Different methods exist for measuring hardness, including Rockwell hardness testing and Brinell hardness testing. These tests utilize standardized indenters while considering factors like load applied and indentation depth measurements.
Torque-to-Yield
Torque-to-yield is another crucial measurement used specifically with internally threaded nuts, such as prevailing torque locknuts or nylon insert locknuts. This measurement indicates the rotational force needed to achieve a specific amount of permanent deformation within the nut.
To conduct a torque-to-yield test, a particular level of torque is applied to the nut until it reaches its yield point, signifying its maximum load capacity. This is crucial in applications where the clamping force must be controlled precisely and maintained throughout its intended service life.
Galvanic Corrosion Resistance
In specific environments with high electrical conductivity, using nuts of different metals can result in galvanic corrosion. For enhanced durability and longevity, selecting nuts that offer excellent resistance to galvanic corrosion is essential.
Laboratory testing involving accelerated corrosion environments or electrochemical test methods can reveal a nut’s resistance to corrosion based on factors like voltage potential and current density measurements.
Fatigue Strength
In real-world applications, nuts often undergo repeated cycles of tightening and loosening forces due to vibrations or dynamic loads. Therefore, it’s essential to consider a nut’s fatigue strength, which measures its resistance to failure under cyclic stress.
Fatigue strength is evaluated through fatigue testing, where the nut is subjected to alternating loading patterns until failure occurs. This measurement helps ensure that the nut can withstand repeated stress without compromising its integrity over time.
Thread Engagement
Thread engagement is the overlap between a nut’s internal and corresponding external threads on a bolt or stud. Sufficient thread engagement is critical for achieving adequate clamping force.
Measuring thread engagement involves determining the number of engaged threads by counting how many complete rotations occur while fully tightening a nut onto a threaded component. Proper thread engagement ensures optimal mechanical grip and prevents potential loosening or stripping under load.
Dimensional Accuracy
Ensuring proper dimensional accuracy in nuts is crucial for compatibility with companion components, such as bolts or studs, providing an effective fit and secure fastening.
Accuracy measurements commonly include evaluating key dimensions like overall diameter, height, width across flats or points (in hexagonal nuts), pitch diameter, and thread quality. These dimensions must conform to industry standards or specifications relevant to your application.
Conclusion
Understanding the strength measurements of hardware nuts is not just a theoretical exercise, but a practical necessity for securely fastening components together.
Tensile strength, yield strength, hardness, torque-to-yield, and galvanic corrosion resistance are not just technical terms, but critical factors that you, as an engineer or construction professional, can use to ensure the performance of nuts in various applications.