What Are The Different Types Of Control Valves Available For Industries?
In the vast and intricate world of industrial automation, control valves play a pivotal role. These devices are the unsung heroes behind precisely regulating fluids, gases, and other mediums in various industrial processes.
Control valves come in many types, each tailored to specific applications and requirements. This comprehensive guide explores the different types of control valves available for industries, shedding light on their features.
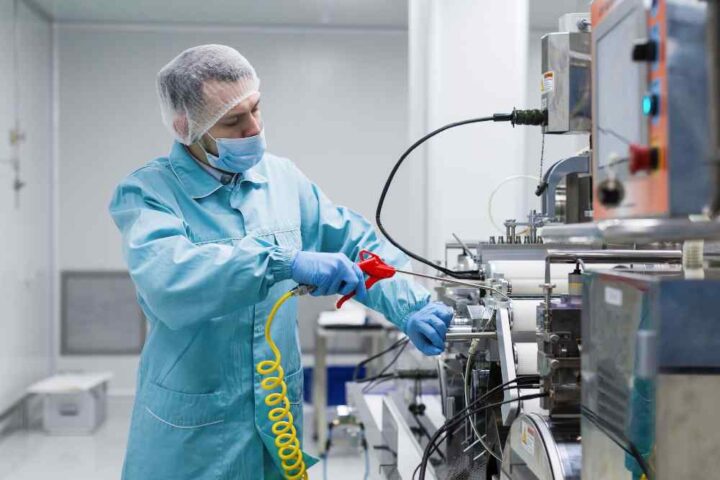
Pneumatic Valves:
Pneumatic valves are a subset of control valves that use compressed air. They are crucial components in pneumatic systems, where air pressure and flow control are essential for various industrial applications. Valves come in various types, including solenoid, diaphragm, and butterfly valves. These valves are known for their reliability, rapid response, and precise control over airflow.
They play a vital role in manufacturing, automotive, and automation industries, where pneumatic systems are employed to power machinery and equipment. These valves are favored for their ability to perform in harsh environments and contribute to efficient and cost-effective industrial processes.
Globe Valves:
Globe valves are essential components in industrial settings, known for their precise control over fluid flow. They consist of a globe-shaped body with a movable plug or disc inside. By adjusting the position of this plug, operators can finely regulate the flow rate. Globe valves are versatile and find applications in power generation, petrochemicals, and HVAC systems. Their ability to provide accurate control makes them indispensable in processes where fluid flow needs to be precisely adjusted.
Butterfly Valves:
Butterfly valves are characterized by their disc-shaped closure element, which pivots around a central axis. These valves are prized for quick on/off operation and are frequently employed in large-diameter pipelines. They excel when considerations such as space and weight are crucial, making them ideal for water treatment plants and the chemical industry. The simplicity of their design allows for easy maintenance and operation.
Ball Valves:
Ball valves feature a spherical closure element, known as the ball, with a hole in the center to regulate fluid flow. Their versatility makes them a staple in various industries, including oil and gas, pharmaceuticals, and food processing. Ball valves are prized for providing tight sealing, ensuring minimal leakage when they are in the closed position. Their straightforward operation and low maintenance requirements make them popular for many applications.
Gate Valves:
Gate valves employ a wedge-shaped gate as the closing element, which can be lowered or raised to control fluid flow. These valves are commonly used in applications requiring full flow or complete shut-off, such as pipelines transporting water, steam, or oil. Gate valves are designed to minimize pressure drop when fully open and are suitable for processes where low friction loss is essential. However, they are not typically used for precise flow control due to their on/off nature.
Check Valves:
Check or non-return valves are essential for preventing backflow in pipelines and systems. They permit fluid flow in one direction while blocking it in the opposite direction. Check valves are crucial when backflow could damage equipment or disrupt processes, such as pump discharge lines. They come in various designs, including swing, lift, and ball check valves, each suited to specific applications.
Pressure Relief Valves:
Pressure relief valves are designed to safeguard equipment and systems from overpressure conditions. When the pressure exceeds a predetermined limit, these valves automatically open to release excess pressure, protecting the system’s integrity. Pressure relief valves are vital for ensuring the safety of various industrial processes, particularly in applications where pressure fluctuations are common.
Diaphragm Valves:
Diaphragm valves utilize a flexible diaphragm to control fluid flow. They are especially valuable in applications where minimizing contamination is critical, such as pharmaceutical and food processing industries. Diaphragm valves provide a tight seal and precise control over flow, making them suitable for handling corrosive or abrasive fluids.
Solenoid Valves:
Solenoid valves are electrically controlled valves that use a solenoid to open or close the valve. They find applications in various scenarios, including irrigation systems, HVAC controls, and automated industrial processes. High-performance solenoid valves are prized for their rapid response time and ease of control, allowing for quick and precise adjustments in fluid flow. They play a crucial role in automating processes and enhancing system efficiency.
Control valves are the unsung heroes of industrial automation, regulating the flow of fluids and gases with precision and reliability. Understanding the different types of control valves and their applications is crucial for industries to optimize their processes, ensure safety, and achieve efficient operation. Whether it’s a globe valve for precise flow control or a pressure relief valve for safeguarding equipment, choosing the right control valve is essential for industrial success.