Thermal Guardians: Exploring the Role of Industrial Temperature Sensors
Temperature control is absolutely essential in a wide range of industrial settings, from bustling manufacturing floors to meticulous food processing plants.
Often overlooked yet crucial, industrial temperature sensors are the unsung heroes that keep these operations ticking along without a hitch. They ensure everything runs smoothly and safely, preventing any unexpected hiccups that could disrupt production.
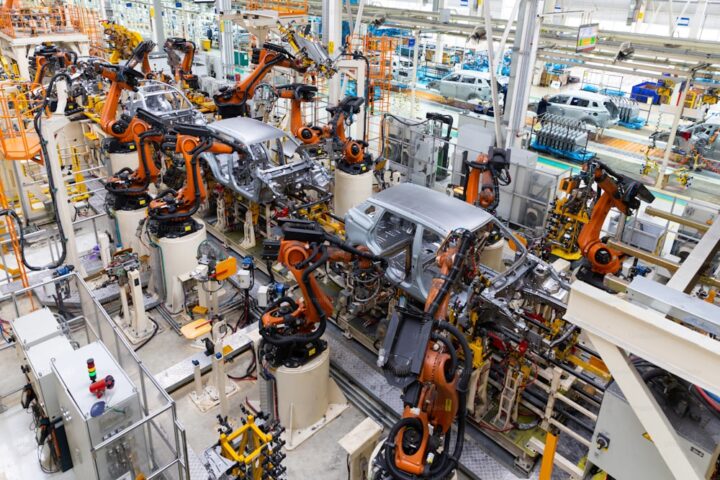
What are Industrial Temperature Sensors?
Defining the Basics
Industrial temperature sensors from the likes of Process Parameters are designed to measure and monitor temperature conditions within an environment or process. These devices are crucial for processes that require precise temperature control, providing feedback that helps maintain optimal conditions.
Types of Sensors
Several types of temperature sensors are used in industry, each suited to specific environments and accuracy needs:
- Thermocouples: Known for their wide temperature range and rapid response time, these are perhaps the most common sensors.
- Resistance Temperature Detectors (RTDs): These offer high accuracy and are typically used where precision is crucial.
- Thermistors: Used for their sensitivity within limited temperature ranges, often in consumer electronics.
- Infrared Sensors: Ideal for non-contact temperature measurements, used where the sensor cannot touch the materials being monitored.
How Do Temperature Sensors Work?
The Science Behind the Sensor
Temperature sensors operate based on physical principles that induce changes in material properties due to temperature variations. For example, a thermocouple generates a voltage that’s directly related to temperature, while an RTD’s resistance changes predictably with temperature fluctuations.
From Data to Decisions
Once a sensor detects a temperature, this data is converted into an electrical signal, which a control system then interprets. This system can trigger alarms, adjust conditions, or shut down operations to prevent damage or ensure product quality.
Applications of Temperature Sensors in Industry
Ensuring Product Quality
In industries like pharmaceuticals and food and beverage, maintaining certain temperatures is essential for safety and quality. Temperature sensors help monitor and document conditions to comply with regulatory standards.
Preventive Maintenance
In machinery and equipment, temperature sensors can detect overheating, a common precursor to mechanical failure. By alerting technicians to potential problems, sensors can prevent costly downtime and repairs.
Energy Efficiency
Optimizing the operation of heating and cooling systems in industrial facilities can lead to significant energy savings. Temperature sensors are key in ensuring systems operate only when necessary and within the most efficient temperature ranges.
Benefits of Using Industrial Temperature Sensors
- Improved Safety: Prevent accidents by detecting abnormal temperatures that could indicate hazardous conditions.
- Enhanced Quality Control: Consistently monitor and adjust processes to maintain product standards.
- Cost Efficiency: Reduce waste and energy consumption by maintaining optimal temperatures.
- Compliance and Documentation: Automated records support compliance with industry regulations.
Choosing the Right Temperature Sensor
Consider the Environment
The choice of sensor largely depends on the environmental conditions it needs to withstand. Consider factors such as the presence of corrosive materials, extreme temperatures, or the need for sanitary conditions.
Accuracy and Response Time
Different sensors offer varying degrees of accuracy and response times. The specific requirements of the process—whether it needs rapid response or extreme precision—will determine the best type of sensor.
Ease of Integration
Consider how easily a sensor can be integrated into existing systems. Compatibility with current data management and control systems is crucial for seamless operation.
Future Trends in Temperature Sensing Technology
Innovation on the Horizon
Here are some key trends that are shaping the future:
- Wireless Technology: Increasingly popular due to their flexibility and reduced wiring costs, wireless sensors can be easily installed in remote or hard-to-access locations.
- Smart Sensors: Equipped with microprocessors, these sensors are capable of more than just temperature detection; they can analyse data and make decisions at the sensor level.
- Increased Durability: Advances in materials science are producing sensors that can withstand harsher environments for longer periods.
- Integration with Predictive Maintenance Systems: Continuously monitoring equipment performance to predict failures before they occur can save significant costs in unplanned downtime.
- Enhanced Accuracy and Sensitivity: The demand for sensors with higher accuracy and sensitivity is growing, with new technologies emerging that offer finer resolution and more precise measurements.
Conclusion
Industrial temperature sensors, or “Thermal Guardians” as we might call them, are vital in the modern industrial sector. They not only ensure safety and quality of products but also enhance operational efficiencies and help meet regulatory demands.
As industries continue to evolve with technological advancements, the role of these sensors will become even more critical. Embracing these guardians of temperature in industrial settings not only supports business operations but also promotes sustainability and safety on a broader scale.
Whether it’s in a steel mill or a microbrewery, temperature sensors ensure that precision and control are always part of the equation.